Introduction to Chinese Porcelain and Its Impact on Europe
The development of Dutch porcelain is a significant chapter in European ceramic history, marked by innovation and adaptation. In the late seventeenth century, Dutch potters began producing tin-glazed earthenware, which came to be known as Delftware, in response to the high demand for Chinese porcelain at the time.
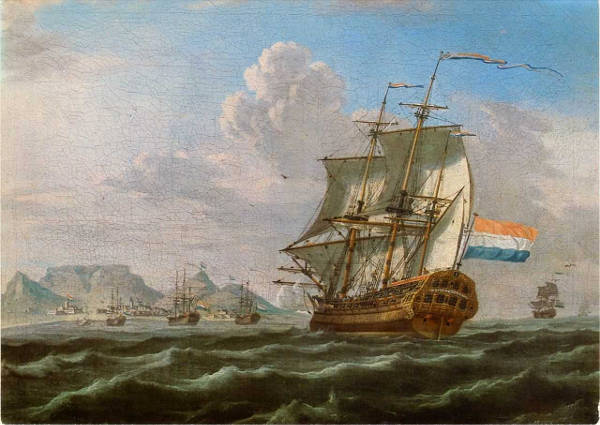
Anonymous (18th century)
c. 1762
Oil on canvas, 34.5 x 45 cm
Iziko William Fehr Collection (Castle of Good Hope), Cape Town
The arrival of late Ming porcelainMing porcelain, produced during the Ming dynasty (1368–1644), is celebrated for its technical innovation, aesthetic refinement, and influence on global ceramics. It represents one of the most significant periods in the history of Chinese porcelain, particularly because of advancements in production techniques and the establishment of standardized methods for large-scale manufacture. in Amsterdam in the early seventeenth century via the VOC (Vereenigde Oostindische Compagnie) (fig. 1), or the Dutch East India Company,The VOC was established in 1602 and became one of the most influential trading entities in global history. Operating until its dissolution in 1799, the VOC was pivotal in the expansion of Dutch commerce and colonial dominance during the 17th and 18th centuries. It was the first multinational corporation and the first to issue shares of stock, making it an early example of modern corporate finance. profoundly influenced Dutch artisans, inspiring the creation of Delftware, a distinctive form of tin-glazed earthenware, offering moreover, exotic motifs for still life and interior Dutch painters.
Chinese porcelain was considered a luxury item due to its rarity and exotic origins. The intricacy of its designs, often featuring floral patterns, landscapes, and mythical motifs, fascinated European consumers. Its association with the distant and mysterious East gave it a sense of exclusivity and sophistication. Owning Chinese porcelain became a status symbol for wealthy Dutch merchants and the upper classes, signaling refinement and worldly connections. Moreover, the quality of Chinese porcelain was unmatched by European ceramics of the time. It was prized for its fine, translucent texture, brilliant white surface, and durability, all achieved through advanced manufacturing techniques unfamiliar to European potters. It was also admired its resilience to heat and liquids, which made it both practical and decorative.
However, civil war in China halted the export of Chinese porcelain, prompting Delft potters to fill the growing demand. By 1670, the pottery industry employed a quarter of Delft's male population, with many manufacturers achieving prosperity. Delftware became a unique adaptation of Chinese porcelain, blending artistic influences with local creativity. Artisans incorporated fine art into their designs, adapting works by skilled painters such as Nicolaes BerchemBerchem, a celebrated Dutch painter and draughtsman, significantly influenced Delftware production through the widespread use of prints based on his works. Renowned for his pastoral landscapes and Italianate scenes, Berchem’s designs were extensively reproduced as etchings and prints during his lifetime, with approximately 190 published. These prints became a vital source of inspiration for Delftware painters, who selectively adapted figures, animals, and pastoral motifs rather than copying entire compositions. Techniques like pouncing allowed artisans to transfer these elements onto ceramic surfaces efficiently. While Berchem did not directly design for pottery, his imagery played a crucial role in shaping the decorative vocabulary of Delftware, illustrating the dynamic relationship between fine art and applied arts in the 17th century. (1620–1683), whose many prints furnished inspiration for Delftware designs, and Leonaert Bramer (1596–1674), who collaborated directly with the pottery establishments.
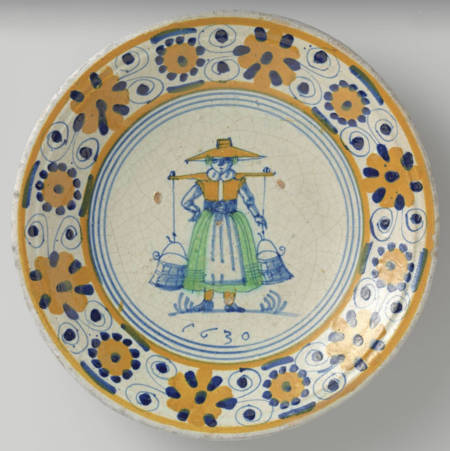
Anonymous, Holland
1630
Maiolica, tin-glazed earthenware with polychrome painted decoration, Diam. 24 cm
Rijksmuseum, Amsterdam
Delft pottery originated in the early fifteenth century in the Netherlands, beginning with simple, locally made red or brown wares that were occasionally decorated with slip patterns and glazed selectively due to the expense of lead glaze. Influenced by luxurious tin-glazed ceramics from Italy, such as Maiolica and Faience, Dutch production evolved in the sixteenth century, particularly with the arrival of Italian potters in Antwerp, who introduced advanced techniques and artistic designs. The Eighty Years' War prompted many Protestant potters to relocate to the northern Netherlands, bringing their expertise to cities like Haarlem and Delft, which became major centers of production. Early Dutch Majolica focused on plates, dishes, and porridge bowls, featuring opaque white tin glaze on the front and a transparent lead glaze on the reverse, often decorated in blue, yellow, and green (fig. 2). These practical yet decorative wares, marked by distinctive spur scars from kiln stacking, provided a refined alternative to primitive wooden utensils, setting the stage for the later prominence of Delftware.
Where in the Netherlands in the early fifteenth century only very simple pottery was being made, various cities in Italy were already producing high quality ceramics. In the cities of Venice, Florence, Faenza and Urbino for example, the potters created ceramics with an opaque white, tin-based glaze on fired clay, which served as a ground for polychrome enamel painting. This South-European pottery, locally referred to as Maiolica or Faience, was richly decorated and coloured.F. T. Scholten, Dutch Majolica & Delftware: The Edwin van Drecht Collection, 1550–1700, exh. cat. (The Hague: Paleis Lange Voorhout, 1993), 11. These wares were transported from Spain and Italy to the Netherlands as early as the 15th century. The finds of Maiolica and Faience in the Netherlands are however very rare, since both the laborious process of painting and the long distance the pottery had to travel, made it a luxury that could only be afforded by a small group of rich people..F. T. Scholten, Dutch Majolica & Delftware: The Edwin van Drecht Collection, 1550–1700, exh. cat. (The Hague: Paleis Lange Voorhout, 1993), 14. The first Dutch Majolica examples, inspired by the southern European wares, can be dated already in the fifteenth century, but it was not until the beginning of the sixteenth century that production took on some proportion..F. T. Scholten, Dutch Majolica & Delftware: The Edwin van Drecht Collection, 1550–1700, exh. cat. (The Hague: Paleis Lange Voorhout, 1993), 14.
The VOC and Porcelain Trade
"Imported Chinese porcelain, commonly referred to as Kraak, Kraak porcelain or Kraak ware (Dutch Kraakporselein),Strictly defined, Kraak is distinguished by the arrangement of its ornament into panels; these usually radiate to a bracketed rim notorious for its liability to chip. It is a sub-class of Jingdezhen ware, mostly made as "deep bowls and wide dishes," decorated with motifs from nature, in a style not used on wares for the domestic Chinese market.Y L. Vinhais and J. Welsh, Kraak Porcelain: The Rise of Global Trade in the 16th and Early 17th Centuries* (London: Jorge Welsh Books, 2008), 147. was first brought to Europe in the sixteenth century when the Portuguese conducted occasional trade with China. It was regarded as a great rarity and reserved as curiosities by kings and nobles, as it had not been sold in substantial quantities in other Western European countries in this period. However, this situation soon changed when the Dutch developed great interest in the trade of Chinese porcelain. In 1602 and 1604, two large cargos of Chinese blue-and-white porcelain loaded on the Sao Tiago and the Santa Catarina, two Portuguese ships, were captured by the Dutch and auctioned in Middelburg and Amsterdam. The sensational interest created by these auctions further stimulated Dutch desire to trade with China."Jing Sun, "Exotic Imitation and Local Cultivation: A Study on the Art Form of Dutch Delftware Between 1640 and 1720," in The Transformation of Vernacular Expression in Early Modern Arts, Intersections, vol. 19 (Brill, 2012).
The term "kraak" is believed to have originated from the Portuguese word "carraca," which referred to large trading ships used by the Portuguese for transporting goods from Asia to Europe.A carrack (Portuguese: nau; Spanish: nao; Catalan: carraca; Croatian: karaka) is a three- or four-masted ocean-going sailing ship that was developed in the 14th to 15th centuries in Europe, most notably in Portugal and Spain. Evolving from the single-masted cog, the carrack was first used for European trade from the Mediterranean to the Baltic and quickly found use with the newly found wealth of the trade between Europe and Africa and then the trans-Atlantic trade with the Americas. In their most advanced forms, they were used by the Portuguese and Spaniards for trade between Europe, Africa and Asia starting in the late 15th century, before being gradually superseded in the late 16th and early 17th centuries by the galleon. Kraak was typically decorated with underglaze blue designs, featuring central motifs such as flowers, birds, or landscapes, surrounded by segmented panels with geometric patterns or floral motifs. The design was well-suited to European tastes and often depicted imagery that appealed to Dutch buyers. Common forms included plates, bowls, and dishes. These were practical for dining and display purposes, aligning with European household uses.
While not always of the highest-grade porcelain compared to imperial Chinese wares, Kraak porcelain was admired for its durability, lightness, and exotic appeal (fig. 3).
The VOC was instrumental in the large-scale importation of Chinese porcelain into Europe. This trade was fueled by both European demand for high-quality ceramics and disruptions in China's domestic economy that made these goods more available for export. Based on official records of the VOC, more than three million pieces of porcelain must have been shipped to Holland by the between 1604 and 1657.
Export production at Chinese Jingdezhen cermaic factories, the most important in China, witnessed yet another boost when the Dutch arrived in China in the early seventeenth century. With the Portuguese well established in Macao, the doorstep to China, the Dutch had repeated disputes with the Portuguese and the Chinese administration. Misbehaving, as the Portuguese did before them, the Dutch were forced to trade along the Chinese coast and from various illegal settlements with primarily Fujian merchants. The difficulties the Dutch had in establishing direct trade with the Jingdezhen potteries is reflected in a letter by Kr. Kohn, an officer of the Dutch VOC company in 1616:
These porcelains sold to us were produced in an inland kiln which was very far away, and those porcelain need to be ordered and paid in advance.Colin Sheaf and Richard Kilburn, The Hatcher Porcelain Cargoes: The Complete Record (Oxford: Phaidon Christie’s Limited, 1988), 24.
"From their various illegal bases on China’s coast, on Taiwan, and at later establishment in Japan, the Dutch had to wait a full year for their deliveries. Yet, despite the distance and with unprecedented trust in the Chinese middlemen, the Dutch alone already in 1608 ordered more than 108,000 pieces of porcelain, a number that grew to 355,800 pieces in 1644, for the European market alone."Colin Sheaf and Richard Kilburn, The Hatcher Porcelain Cargoes: The Complete Record (Oxford: Phaidon Christie’s Limited, 1988), 25.
The VOC's Role
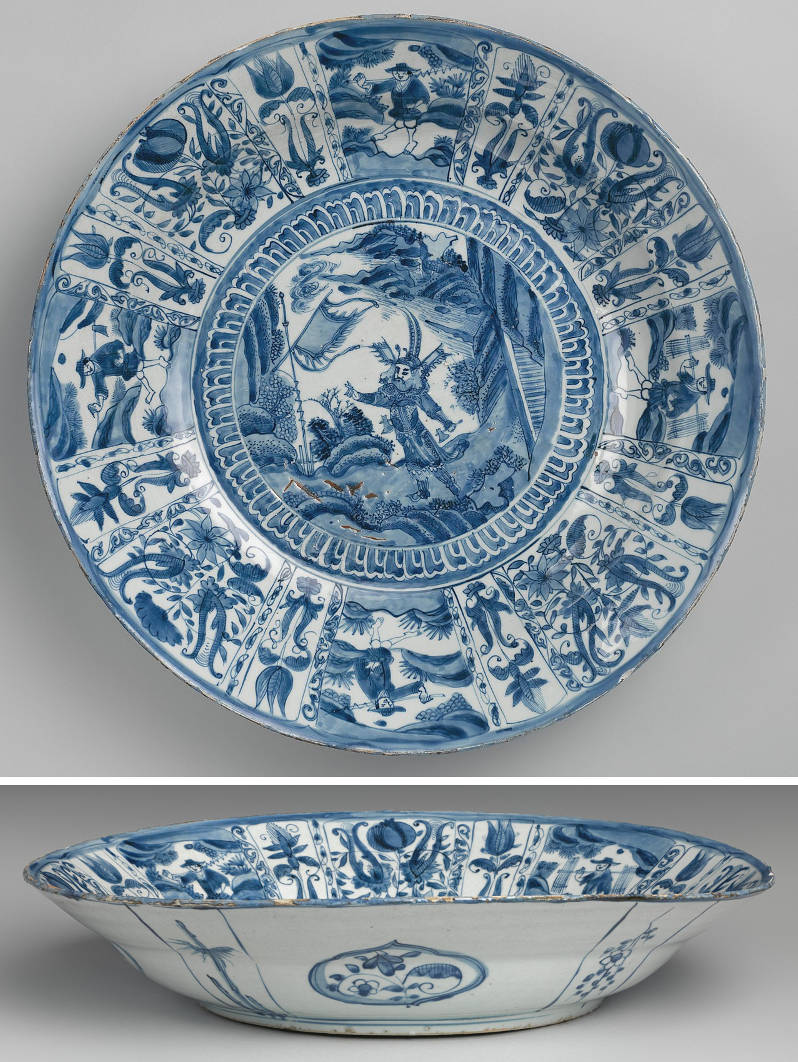
Anonymous
Ming dynasty (1368–1644)
Porcelain painted with cobalt blue under a transparent glaze , h. 10.2 x Diam. 47.3 cm; diam. of foot 26.7 cm.
Metropolitan Museum of Art, New York
Before the Dutch gained direct access to Chinese markets, the Portuguese dominated the porcelain trade in Europe. "The Dutch initially acquired Kraak porcelain and other Oriental goods through piracy, seizing ships laden with valuable cargo. For example, in the early 1600s, the Dutch captured Portuguese vessels, such as the Santa Catarina in 1603, loaded with Chinese porcelain. These spoils were auctioned in the Netherlands, sparking intense interest in Chinese goods among Dutch consumers and merchants. Over time, however, the Dutch recognized that direct trade with China would be far more lucrative and sustainable than piracy. This realization led to the establishment of formal trading routes and agreements through the VOC. The VOC began importing Chinese porcelain on a large scale, supplying the growing European demand and integrating these exotic goods into Dutch households and artistic traditions. By importing these items directly, the Dutch ensured a steady and profitable supply while fostering economic and cultural exchanges with Asia."Timothy Brook, "A Dish of Fruit," in Vermeer's Hat: The Seventeenth Century and the Dawn of the Global World (New York: Bloomsbury Press, 2008), 55–84.
Between 1602 and 1682, it is estimated that the VOC imported millions of pieces of Chinese porcelain into Europe. A single shipment might contain tens of thousands of items, illustrating the scale of the operation. Porcelain was sometimes used as ballast for ships carrying spices and other valuable goods, further integrating it into VOC trade.
However, the fall of the Ming dynasty in 1644The fall of the Ming dynasty in 1644 marked the end of nearly three centuries of rule by one of China's most influential dynasties. A combination of internal and external factors led to its collapse. Internally, the Ming government suffered from widespread corruption, ineffective leadership, and fiscal mismanagement, exacerbated by the high costs of defending the empire from constant threats. Natural disasters, famine, and heavy taxation further destabilized the population, fueling widespread rebellions such as the peasant uprising led by Li Zicheng. Externally, the Manchu forces of the rising Qing dynasty capitalized on this internal turmoil. When Li Zicheng's forces captured Beijing, the last Ming emperor, Chongzhen, committed suicide, and the Manchu seized the opportunity to ally with Ming loyalists to enter the city, establishing Qing rule and ending the Ming era. and subsequent political instability in China disrupted porcelain production and trade. This temporarily reduced the availability of Chinese porcelain, prompting the Dutch to develop local alternatives. When trade resumed, Chinese porcelain remained in high demand but had to compete with these domestic imitations.
Kraak produced in Jingdezhen destined for export was transported with relative ease on the Chang RiverThe Chang River, also known as the Yangtze River, is the longest river in Asia and the third longest in the world, stretching over 6,300 kilometers. Flowing through diverse terrains, from the Tibetan Plateau to the East China Sea, the river is a vital artery of China's geography, economy, and culture. Historically, it has supported agriculture, transportation, and trade, while its fertile basin has nurtured countless civilizations. Today, the Chang River remains central to China's development, hosting major cities along its banks, including Shanghai, and serving as a key waterway for commerce and energy generation through projects like the Three Gorges Dam. and its tributaries. One Ming official, Miu Zongzhou, wrote that "Kilns are arranged along the rivers and boats and ships which carry porcelain come and go everyday." Despite Jingdezhen's location in the remote corner of Jiangxi province, these boats and ships managed to transport huge volumes of ceramics to domestic markets as far away as Beijing as well as to different seaports for shipping overseas.Sten Sjostrand, "Jingdezhen, 'The Porcelain Centre of the World': A Short Description of the History, Developments, Transport, and Production of Ancient Chinese Porcelain," Nanhai Marine Archaeology, accessed November 30, 2024, http://www.thewanlishipwreck.com/Jingdezhen.html.
Jingdezhen is part of China’s extensive river network, one of which ultimately leads to the port of Macau, the point from which Dutch cargo ships transported goods to Europe. Goods from Jingdezhen were first transported via the Chang and Gan Rivers to Poyang Lake, which connects to the Yangtze River. From there, porcelain could be shipped downstream and then transferred overland or via smaller rivers to the Pearl River Delta, where Macau is located. The Pearl River serves as Macau's main waterway and connects to a broader network of inland rivers and canals. However, no single continuous river directly links Jingdezhen and Macau; the journey required a combination of river navigation and overland transport.
The sea voyage from Macau to the Netherlands, via the VOC shipping routes, typically took six to nine months depending on the season, weather conditions, and stopovers (e.g., at the Cape of Good Hope or Batavia, modern-day Jakarta). However, from the moment an order was placed in the Netherlands to the time the goods arrived back, the process could take two to three years on average. This timeline includes the round-trip sea voyage, procurement time in Macau, and delays inherent in communication and logistics.
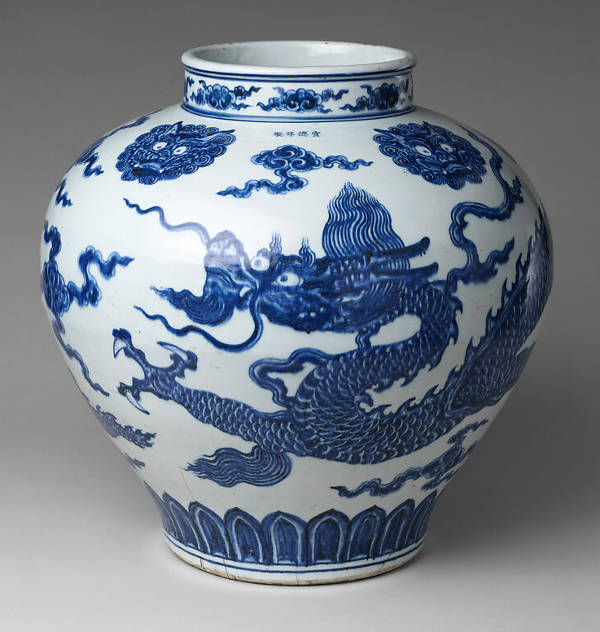
Anonymous
c. early 15th century
Porcelain painted with cobalt blue under transparent glaze (Jingdezhen ware), H. 48.3 x Diam. 48.3 cm
Metropolitan Museum of Art, New York
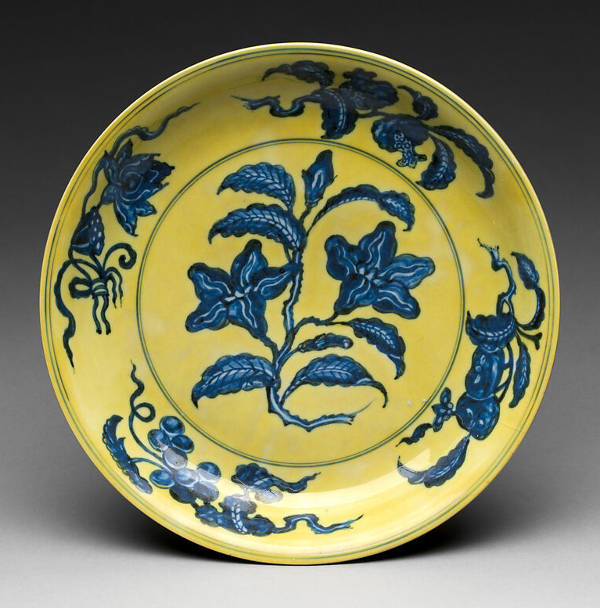
Anonymous
Late 16th century
Porcelain painted with cobalt blue under and colored enamel over transparent glaze (Jingdezhen ware), Diam. 26 cm
Metropolitan Museum of Art, New York
The Quality of Imported Kraak
The quality of imported Kraak ware is much disputed among scholars; some claim that it is surprisingly good, in certain cases indistinguishable from that produced for the domestic Chinese market;David Howard and John Ayers, China for the West: Chinese Porcelain and Other Decorative Arts for Export, Illustrated from the Mottahedeh Collection (London and New York: Sotheby Parke Bernet, 1978), 11. others imply that it is a dismal shadow of the truly fine ceramics China was capable of producing.Rosemary Kerr, "Early Export Ceramics," in Chinese Export Art and Design , ed. Craig Clunas (London: Victoria and Albert Museum, 1987), 38. Rinaldi comes to a more even-handed conclusion, noting that it "forms a middle category between much heavier wares, often coarse, and definitely finer wares with well levigated clay and smooth glaze that does not shrink on the rim..." Thus looking at ceramic production in China at the time from a broader prospective, Kraak ware falls between the best examples and a typical provincial output, such as the contemporary Swatow ware,Swatow ware is a type of Chinese export pottery produced primarily during the late Ming dynasty (16th–17th centuries). Its name comes from the port of Swatow (modern-day Shantou) in Guangdong Province, which was historically associated with its trade, though most of the ware was produced in kilns in Fujian Province. Swatow ware is distinctive for its bold decoration, coarse craftsmanship, and specific use as an export product aimed at Southeast Asian and other foreign markets. also made for export, but to South-East Asia and Japan.Maura Rinaldi, Kraak Porcelain: A Moment in the History of Trade (London: Bamboo Publishing, 1989).
Adaptation and Innovation
In any case, Chinese manufacturers soon began supplying specifically tailored Kraak designed to meet European demand, which sometimes differed significantly from domestic Chinese preferences. This was not a matter of deception but rather a pragmatic trade strategy. The porcelain produced for export could be made more quickly and in large quantities, prioritizing efficiency over the refinement typically reserved for pieces intended for the Chinese elite or the imperial court. European buyers, unfamiliar with the highest standards of Chinese porcelain, valued the exotic appeal and craftsmanship of these goods, which still far surpassed anything produced in Europe at the time. Nonetheless, the mass production of Kraak did not deter the Dutch, as even lower-grade porcelain was superior to European alternatives like tin-glazed earthenware. It was also more affordable and allowed the VOC to purchase large quantities to meet the booming demand in Europe, where consumers were drawn to the novelty and prestige of owning Chinese porcelain. Records show that the Dutch often placed specific orders for designs they knew would appeal to their buyers, focusing more on marketability than on acquiring the finest porcelain. For both the Chinese producers and Dutch traders, this arrangement was mutually beneficial, ensuring a steady flow of goods and profits while cementing porcelain's status as a luxury item in seventeenth-century Europe. Potters at Jingdezhen adapted designs to meet European tastes, even incorporating tulip motifs during the height of the Dutch tulip craze in the 1620s. This responsiveness underscores the dynamic interplay of global trade, consumer demand, and artistic adaptation during the early modern period.Timothy Brook, Vermeer's Hat: The Seventeenth Century and the Dawn of the Global World (New York: Bloomsbury Press, 2008).
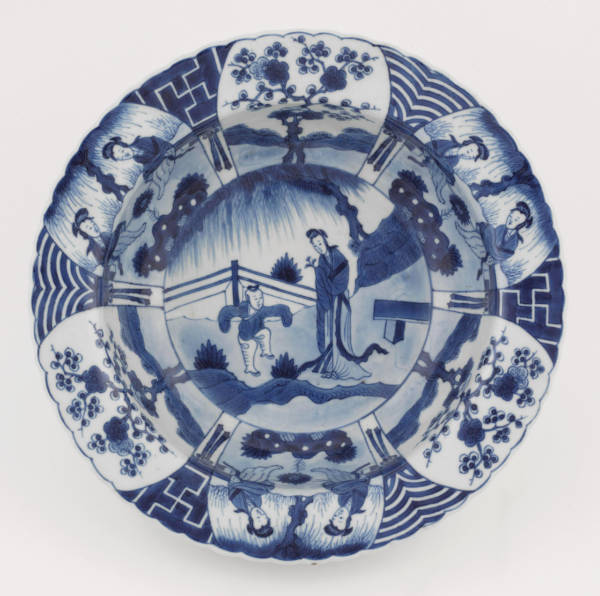
Anonymous Chinese
c. 1662–1722 (Kangxi period)
Porcelain, H. 7 x Diam. 26.5 cm
Centraal Museum, Utrecht, Netherlands
One prominent example of the Kraak market adaptability is the production of klapmutsen, a type of bowl designed for Dutch use (fig. 4). Unlike traditional Chinese bowls, which had high walls and no rims, klapmutsen featured broader bases and wide, flat rims. These modifications accommodated European dining habits, particularly the use of heavy, long-handled metal spoons for soups and stews. The rim of the klapmuts provided a convenient resting place for spoons, preventing them from toppling into the bowl. This form was largely absent in Chinese domestic markets, indicating that it was created specifically for export.
In addition to structural changes, Chinese potters tailored decorative elements to align with European tastes. While early export wares often featured traditional Chinese motifs, such as dragons or landscapes, later pieces included imagery inspired by European culture, including coats of arms, floral patterns familiar to European audiences, and even biblical scenes.
Production of Chinese Porcelain
In the 1600s, Chinese porcelain production represented a pinnacle of craftsmanship and innovation, blending artistic mastery with advanced technological processes. Centered in Jingdezhen, the industry thrived on the region's abundant resources, including high-quality kaolin clay and access to sophisticated kilns capable of reaching extreme temperatures.
Kaolin clay, also known as "china clay," was is a fundamental component of imported Chinese porcelain production, significantly influencing its properties and quality. Porcelain is typically composed of a mixture of kaolin, feldspar, and silica. Kaolin serves as the primary clay material, providing the necessary plasticity for shaping and molding. Its fine particle size and purity contribute to the workability of the ceramic body. During firing, kaolin undergoes a transformation, contributing to the formation of mullite crystals. This crystalline structure enhances the mechanical strength and durability of the porcelain. The high fusion temperature of kaolin also allows for the production of ceramics that can withstand significant thermal stress. The naturally bright white color of kaolin imparts a desirable whiteness to porcelain, which is often associated with high-quality ceramics. Additionally, the purity of kaolin, with low concentrations of iron and other impurities, ensures minimal discoloration, resulting in a translucent and aesthetically pleasing final product.
Lacking access to the kaolin clay essential for true porcelain, Delft potters employed a method involving tin-glazed earthenware. They applied an opaque white glaze containing tin oxide to earthenware, creating a smooth, white surface suitable for painting. Artisans then painted designs using cobalt oxide, which produced a vivid blue color upon firing, mimicking the blue-and-white aesthetic of Chinese porcelain. The pieces were subsequently fired at high temperatures to fuse the glaze and decoration, resulting in a durable finish.
"The arrival of Chinese Kraak porcelain in the Dutch market presented significant challenges to local majolica potters, who were unable to replicate the strength, thinness, and visual appeal of these exotic wares. In response, Dutch potters adopted four distinct strategies to adapt to the new competition. Some potters, unable to compete, chose to abandon their craft altogether and liquidate their businesses. Others shifted their focus to the production of tiles, a market segment unaffected by Chinese imports. These tiles were often decorated with contemporary designs, albeit less innovative than other ceramics, and catered to a stable local demand. A third group responded by producing inexpensive earthenware aimed at lower social classes. These wares, though less polished and often decorated with simple, tile-like patterns, offered a cost-effective alternative to imported porcelain. The final and most transformative response came from potters who sought to imitate Chinese Kraak porcelain. While they lacked kaolin, a key ingredient for making true porcelain, Dutch potters developed "Delffse porceleyn," or Delftware, which visually resembled the coveted Chinese imports."Chinese Kraak-Porcelain and its Dutch Counterpart," Aronson Delftware, accessed November 28, 2024, https://www.aronson.com/chinese-kraak-porcelain-and-its-dutch-counterpart-2/.
The Emergence of Japanes Porcelain TradeChristine Corbieler, China Trade: Porcelain Patterns of Exchange (New Haven: Yale University Press, 2006), 20-21.
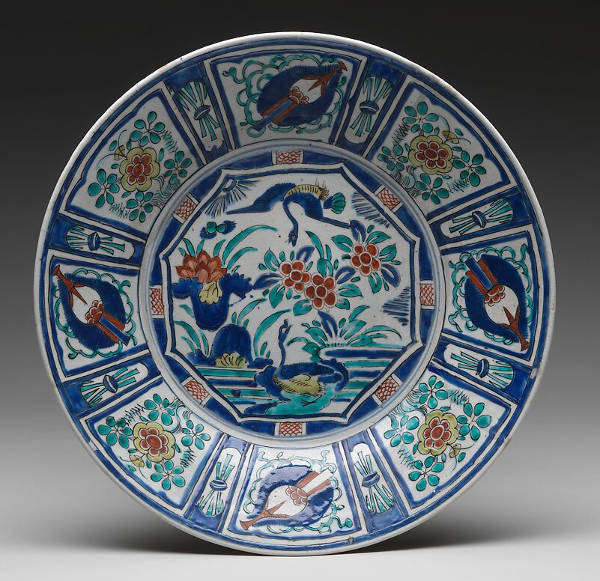
Anonymous
c. 1660–1680
Porcelain painted with colored enamels over transparent glaze (Hizen ware), H. 6.2 x Diam. 32.4 cm; Foot Diam. 14.6 cm
The Metropolitan Museum of Art, New York
The emergence of Japanese porcelain in the seventeenth century was a significant development in the global ceramics trade. Before this period, China was the dominant producer of high-quality porcelain, supplying a vast market that included Europe, the Middle East, and other parts of Asia. However, during the early seventeenth century, internal strife in China, including the fall of the Ming dynasty and the subsequent disruptions in porcelain production, created an opportunity for Japan to enter the market. Other European nations, including Portugal and England, also traded in Chinese porcelain, but the Dutch dominated the market for Japanese exports. Over time, as Chinese production resumed and grew under the Qing dynasty, China regained its position as the dominant supplier of export porcelain to Europe.
The origins of Japanese porcelain production can be traced to the discovery of kaolin clay near Arita in the early seventeenth century.Arita, a small town in Japan's Saga Prefecture, became a pivotal center for porcelain production in the early 17th century following the discovery of kaolin clay in the area. This clay, essential for creating porcelain, was found by Korean potters who had been brought to Japan during the Imjin War (1592–1598). The availability of kaolin allowed Japanese artisans to develop their first true porcelain, marking a significant milestone in Japanese craftsmanship. Arita's potters initially emulated Chinese designs, particularly the blue-and-white porcelain popular in global trade, but they soon developed their own distinctive styles, such as Kakiemon and Imari ware. These innovations transformed Arita into a thriving hub for porcelain production and export, setting the stage for Japan’s emergence as a major player in the global ceramics trade during the 17th century. This material was essential for creating porcelain, and its availability allowed Japanese potters to experiment with and eventually master the craft. Techniques and designs were heavily influenced by Chinese porcelain, especially the blue-and-white wares that were highly prized in global trade. Japanese artisans adapted these techniques to their own cultural aesthetics, resulting in distinctive styles such as the bold and colorful Kakiemon and Imari wares.
The European demand for porcelain during this period was immense, driven by the VOC and other European trading powers. For example, a modest still life or landscape might cost about 10–20 guilders, whereas high-quality silver or porcelain items of a similar size and complexity could reach 50– 100 guilders or more. When Chinese exports waned, Japanese porcelain filled the gap, becoming a major export commodity. Imari porcelain, in particular, became highly popular in Europe for its vibrant palette and intricate designs, often featuring floral and geometric motifs. These pieces not only satisfied European tastes but also influenced local pottery traditions, leading to the imitation of Japanese styles.
Japanese porcelain also played a crucial role in East Asian trade networks. It was shipped to Southeast Asia and the Middle East, where it was valued for its quality and artistic appeal. The success of Japanese porcelain in the seventeenth century marked a shift in the dynamics of global ceramics production, establishing Japan as a significant player in this prestigious and lucrative industry. This period laid the foundation for Japan's enduring reputation as a producer of fine porcelain and influenced the evolution of global decorative arts.
B
- Banding Wheel: A manually operated, rotating platform used by potters to decorate or shape ceramic pieces uniformly. It allows for precise control when applying decorations or trimming.
- Bisque: Unglazed ceramic ware that has undergone bisque firing. It is porous and ready to accept glaze applications.
- Biscuit firing: The initial firing of unglazed earthenware, which produces biscuit wares.
- Body: Fired clay with no glaze or enameling.
C
- Casting Slip: A liquid mixture of clay and water with added deflocculants used in slip casting to form ceramic objects in plaster molds.
- Chamotte clay: Pre-fired clay that is added to raw clay used to make pots to produce a stronger body.
- Charger: Chargers have a diameter of 26 centimeters or more. Smaller versions are generally referred to as plates.
- China Clay: Another term for kaolin, the primary clay used in porcelain production due to its purity and whiteness.
- Chinoiserie: The use of motifs derived from Chinese art to give objects made in Western Europe an "exotic" appearance. The Delft pottery industry was instrumental in establishing this fashion.
- Craquelure (crackle): Hairline cracks in the glaze caused during glaze firing as the glaze and body shrink at different rates.
- Creamware: A hard type of earthenware with a cream-colored body covered with a transparent lead glaze.
- Crystalline glaze: Glaze with small crystals on the surface formed as a result of gradual cooling of metal oxides in the glaze.
D
- Delftware: English term for tin-glazed earthenware, referencing the Dutch town of Delft. Capitalized, it refers specifically to Delft earthenware; lowercase refers to tin-glazed earthenware made anywhere.
E
- Earthenware: A type of ceramic with a porous body, created at firing temperatures of approximately 800–1150°C. Must be glazed to be watertight.
- Eggshell porcelain: Porcelain with extremely thin walls, often translucent, resembling eggshells.
- Enamel: Vitreous pigment (either opaque or transparent) that is coloured with metal oxides applied to the surface of ceramics, typically as overglaze decoration requiring a lower-temperature firing.
F
- Factory mark: A mark referring to the pottery, usually referencing the name of the pottery or its proprietor or manager.
- Faience: Tin-glazed earthenware, often with a thin body and smooth front surface.
- Familles: Enamelled Chinese porcelain is traditionally divided into different colour families (‘famille’ being French for family): vert (green), rose (pink), noir (black) and jaune (yellow). These categories were defined in Europe in the 19th century.
- Feldspar: A group of minerals used in ceramic bodies and glazes as a flux to lower the melting point.
- Firing;The entire process of heating and cooling off pottery in the kiln. There were usually two firings: the biscuit firing and the glaze or glost firing.
- Flatware: Collective term for flat items like plates and platters, to distinguish them from hollow wares. >
- Flux: A material that promotes melting or fusion in glazes and clay bodies by lowering the melting point of silica.
- Foot Ring: The circular base of a ceramic piece, often left unglazed to prevent it from fusing to kiln shelves during firing.
G
- Glaze: Vitreous layer on the surface of ceramics.
- Glaze or Glost Firing: The second firing, designed to fuse the glaze to the surface at a temperature of approx. 1000° C. To prevent objects from fusing together in the kiln, they are separated using spurs or pegs and saggars.
- Grand feu technique: The process of firing objects at approximately 1000°C, often during the second (glaze or glost) firing.
I
- Imari porcelain: Type of Japanese porcelain whose decorative style, named after the port of Imari, was imitated in (a.o. China and also) Delft. The blue, red and gold porcelain first appeared on the Dutch market around 1680.
K
- Kakiemon porcelain: Type of Japanese porcelain whose decorative style was imitated in Delft, among other places. The multicoloured porcelain with refined decoration (named after a family of potters) first appeared on the Dutch market around 1680.
- Kangxi porcelain: Type of Chinese porcelain developed during the Kangxi period in the Qing dynasty (1662-1722).
- Kaolin or China clay: A type of clay essential for porcelain production.
- Kendi: Jug with a round body. The neck or spout sits on the rounded shoulder. Some are in the shape of animals (including elephants, ducks and fish). Kendi were used throughout Southeast Asia and the Middle East. A porcelain version of this form was introduced to the Netherlands in the early 17th century.
- Kraak ware or Kraak porcelain (see Wanli porcelain): A type of Chinese porcelain made in the time of Emperor Wanli (1573-1619) and his successors, right through to the fall of the Ming dynasty in 1644. The distinctive blue decoration is divided into panels and applied on a white ground.
- Kwaarten: Traditional Dutch term for the application of a top layer of transparent lead glaze (kwaart) to produce a brilliantly shiny surface. Also known as coperta.
L
- Lead glaze: A transparent glaze whose main component is lead oxide.
- Leather-hard: The stage of clay dryness where it is firm yet still retains moisture, allowing for carving, joining, and trimming without distortion.
- Lustre glaze: Glaze with a metallic shine, obtained by the addition of metal oxides.
M
- Majolica: Tin-glazed earthenware with a layer of tin glaze on the front and transparent lead glaze on the back.
- Maker’s mark: A mark used by a craftsman to show the workshop where objects were made.
- Marl: Adding earth from Tournai (known in Dutch as Doornikse aarde) to clay produced a pale yellow body.
- Molding: Forming ceramic pieces by pressing clay into a rigid mold, allowing for the production of uniform shapes.
- Monochrome: Decoration in a single colour. In Delft usually blue.
- >Muffle kiln: Small kiln used to fire smaller batches of pots. Some gilders had kilns of this type on the premises, presumably to fire gilded pieces using the petit feu technique. Hence the Dutch term ‘goudschilderoven’ (= gilder’s kiln).
O
- On-glaze: Decorative enamels applied over the glaze layer and fired at low temperatures to fuse the decoration without affecting the underlying glaze.
- Oxidation firing: Allowing oxygen in during the glaze firing so that clay containing iron oxide, for example, turns red.
P
- Pâte-sur-pâte: Decoration produced on porcelain using semi-liquid white porcelain slip, sometimes tinted with metal oxides.
- Petit feu technique; The process of firing objects at a temperature of approx. 600° C. This was usually done in small muffle kilns, known in Dutch as goudschilderovens (= gilders’ kilns), used for gilded objects and delicate colours that would be incinerated at higher temperatures.
- Plate: Plates have a diameter of up to 26 centimeters. Larger plates can also be referred to as platters.
- Plateel:Contenporary term for lead- and tin-glazed earthenware (majolica and faience). Also used to reference typical wares produced in the Netherlands in the early twentieth century.
- Plateelbakker: Dutch term meaning a producer of lead- and tin-glazed earthenware (majolica and faience).
- Plateelbakkerij: Dutch term for a pottery producing lead- and tin-glazed earthenware (majolica and faience).
- Plateelschilder: Dutch term for a painter specially trained to decorate earthenware.
- Polychrome: Decoration in more than one colour.
- Porcelain: Type of ceramic with a hard, non-porous body created by firing at a temperature of 1300-1500 ºC.
- Porceleyn (Porceleyne, porcellyne etc.): The old name used in Delft for tin-glazed earthenware that was meant to imitate porcelain.
- Pounce: Paper on which the outlines of a decorative design have been pricked out. The design is transferred to the object through the holes using powdered charcoal.
- Porcelain: A type of ceramic with a hard, non-porous body, fired at temperatures of 1300–1500°C.
R
- Reduction firing: A technique whereby the amount of oxygen entering the kiln during glaze firing (at a relatively high temperature) is reduced in order to produce colour variations and textured effects in the glaze.
- Running glaze: Glaze with a low melting point that runs when fired. Running glazes are applied on top of a glaze with a higher melting point.
S
- Saggar: A cylindrical earthenware container in which earthenware objects would be stacked for firing. To prevent the objects from fusing to the surface, each one would rest on triangular pegs inserted through the wall of the saggar. To protect the pots from kiln fumes, the saggar was closed during firing by placing tiles on top and underneath.
- Sgrafitto: Technique whereby decoration is incised into the surface of a ceramic object that is covered with a layer of slip (engobe).
- Shrinkage: The reduction in size of a clay body during drying and firing due to loss of water and densification of particles.
- Sinter engobe: A blend of engobe and a vitreous substance that produces a glaze-like shine on a ceramic object.
- Slip: Liquid clay used as an adhesive to stick together the different parts of an object during the production process.
- Slip Casting: Forming ceramic objects by pouring slip into a plaster mold, which absorbs water and forms a solid layer against the mold walls.
- Spur: Ceramic support used to separate pieces of majolica in the kiln during glaze firing and stop the pieces fusing together.
- Spur mark: Scar on the front of a piece of majolica caused by the spur used to support it in the kiln.
- Stoneware: Hard, non-porous ceramic fired at approximately 1200–1300°C.
T
- Thrower: A craftsman who makes objects on a potter’s wheel.
- Throwing: The process of shaping clay on a potter's wheel by hand while it spins, allowing for symmetrical forms. Tin glaze bath: Tub containing tin glaze into which the wares (biscuit) are dipped after the first firing, creating a white surface to which the painter can then apply the decoration.
- Transfer printing: Technique whereby a design printed on prepared paper is transferred to the surface of a ceramic object.
- Transitional porcelain: Blue-and-white Chinese porcelain produced in the period of transition between the Ming and Qing dynasties (during the reign of Emperor Shunzhi between 1644 and 1661). Its decoration is characterised by continuous narrative scenes.
- Translucency: The property of allowing light to pass diffusely through a material; in porcelain, it is a valued aesthetic quality.
- Throwing: The process of shaping clay on a potter's wheel by hand while it spins, allowing for symmetrical forms.
W
- Wanli porcelain: A type of Chinese porcelain from the time of Emperor Wanli (1573–1619), characterized by distinctive blue decoration.
- Wheel: A potter's wheel, a device that spins clay to facilitate the shaping of symmetrical ceramic forms.
X
- XRF: Research technology based on x-ray fluorescence used to measure the composition of materials, increasingly in studies of Delftware.
Bibliography
- Bang, Byung Sun. "Influence of Chinese Export Porcelain on Delftware during the Dutch Republic Era." Art History Journal 48 (June 15, 2017): 311–35.
- Carswell, John. Blue and White: Chinese Porcelain and Its Impact on the Western World. Exhibition Catalogue. Chicago: David and Alfred Smart Gallery, 1985.
- Caiger-Smith, Alan. Tin-Glaze Pottery in Europe and the Islamic World: The Tradition of 1000 Years in Maiolica, Faience and Delftware. London: Faber and Faber, 1973.
- Crowe, Yolande. Persia and China: Safavid Blue and White Ceramics in the Victoria and Albert Museum, 1501–1738. London: Victoria & Albert Museum, 2002.
- Hochstrasser, Julie. Still Life and Trade in the Dutch Golden Age. New Haven and London: Yale University Press, 2007.
- Howard, David, and John Ayers. China for the West: Chinese Porcelain and Other Decorative Arts for Export, Illustrated from the Mottahedeh Collection. London and New York: Sotheby Parke Bernet, 1978.
- Jörg, Christiaan J.A. Porcelain from the Vung Tau Wreck: The Hallstrom Excavation. Singapore: Sun Tree Publishing, 2001.
- Kerr, Rosemary. "Early Export Ceramics." In Chinese Export Art and Design, edited by Craig Clunas. London: Victoria and Albert Museum, 1987.
- Kroes, Jochem. Chinese Armorial Porcelain for the Dutch Market: Chinese Porcelain with Coats of Arms of Dutch Families. Den Haag: Centraal Bureau voor Generalogie and Zwolle: Waanders Publishers, 2007.
- Pluis, Jan. The Dutch Tile: Designs and Names 1570–1930. Nederlands Tegelmuseum – Friends of the Museum of Otterlo Tiles. Leiden: Primavera Pers, 1997.
- Rinaldi, Maura. Kraak Porcelain: A Moment in the History of Trade. London: Bamboo Publishing, 1989.
- Savage, George. Pottery Through the Ages. London: Penguin, 1959.
- Vainker, S.J. Chinese Pottery and Porcelain. London: British Museum Press, 1991.
- Wu, Ruoming. The Origins of Kraak Porcelain in the Late Ming Dynasty. Weinstadt: Verlag Bernhard Albert Greiner, 2014.
- Wuestman, Gerdien. "Wouwerman on Delftware." Rijksmuseum Bulletin57, no. 3 (September15, 2009): 236–43.